In the dynamic world of manufacturing, Manufacturing Property Inspectionsreign supreme. Every cog in the machine, from raw materials to finished products, needs meticulous attention to detail. But often overlooked in this intricate dance is the foundation itself:
the manufacturing property. A thorough inspection of this crucial space is like a doctor's examination for your business, revealing potential issues that could hinder production, safety, and ultimately, your bottom line.
This guide delves deep into the world of manufacturing property inspections, equipping you with the knowledge to make informed decisions and ensure your facility thrives. We'll explore the reasons for conducting inspections, the different types available, and the key aspects to be scrutinized. By the end, you'll be able to confidently navigate the inspection process, optimize your property, and safeguard your manufacturing journey.
Why Inspect?
Manufacturing property inspections are not just a formality; they are vital investments in your business's success. Here's why:
Safety First: A comprehensive inspection identifies potential safety hazards like faulty electrical wiring, malfunctioning machinery, or structural deficiencies. This proactive approach minimizes risks of accidents, injuries, and costly lawsuits.
Enhanced Efficiency: A comprehensive inspection identifies potential safety hazards Leaky roofs, outdated equipment, or inadequate ventilation can hamper production flow and waste valuable resources. Identifying these issues allows for timely repairs and upgrades, leading to smoother operations and increased productivity.
Cost Optimization: Early detection of problems saves money in the long run. Addressing minor issues before they escalate into major repairs prevents hefty unplanned expenses and production downtime.
Compliance: Manufacturing facilities must adhere to a multitude of regulations, from environmental standards to building codes. Inspections ensure your property complies with these regulations, avoiding fines, penalties, and reputational damage.
Informed Decision-Making: Whether you're buying, selling, or leasing a manufacturing property, a thorough inspection provides invaluable insights into its condition and potential future costs. This knowledge empowers you to make informed decisions and negotiate effectively.
Types of Inspections:
The type of inspection you need depends on your specific needs and goals. Here are some common options:
Pre-purchase Inspection: This is a must-have for anyone considering buying a manufacturing property. It provides a detailed assessment of the building's structural integrity, mechanical systems, electrical wiring, plumbing, and environmental hazards.
Pre-lease Inspection: Similar to a pre-purchase inspection, this helps you understand the condition of a property before signing a lease agreement. It's crucial for identifying potential maintenance responsibilities and negotiating lease terms.
Pre-sale Inspection: Proactive sellers can use this inspection to identify and address any issues before putting the property on the market. This can increase the property's value and attract more potential buyers.
Routine Maintenance Inspection: Regular inspections help you stay ahead of potential problems and ensure your property remains in top condition. This proactive approach minimizes downtime and extends the lifespan of your equipment and infrastructure.
Targeted Inspection: This focuses on specific areas of concern, such as roof leaks, electrical problems, or machinery malfunctions. It's a cost-effective option for addressing specific issues without the need for a full-blown inspection.
Key Aspects of the Inspection:
Regardless of the type of inspection, certain key aspects will always be scrutinized:
Building Structure: This includes the foundation, walls, roof, and any structural elements. Inspectors will assess for cracks, leaks, deterioration, and compliance with building codes.
Mechanical Systems: This encompasses HVAC systems, plumbing, electrical wiring, and fire protection equipment. The inspector will check for functionality, efficiency, and safety hazards.
Environmental Concerns: This includes asbestos, lead paint, mold, and other hazardous materials. Inspectors will also assess waste disposal practices and compliance with environmental regulations.
Safety Compliance: This covers fire safety systems, emergency exits, machine guarding, and adherence to safety protocols.
Accessibility: The inspector will ensure the property complies with accessibility regulations for people with disabilities.
Beyond the Checklist:
A good inspection goes beyond simply ticking boxes. A qualified inspector will look for underlying issues, assess potential risks, and offer recommendations for improvement. They will also be able to explain their findings in a clear and concise way, ensuring you understand the implications and can make informed decisions.
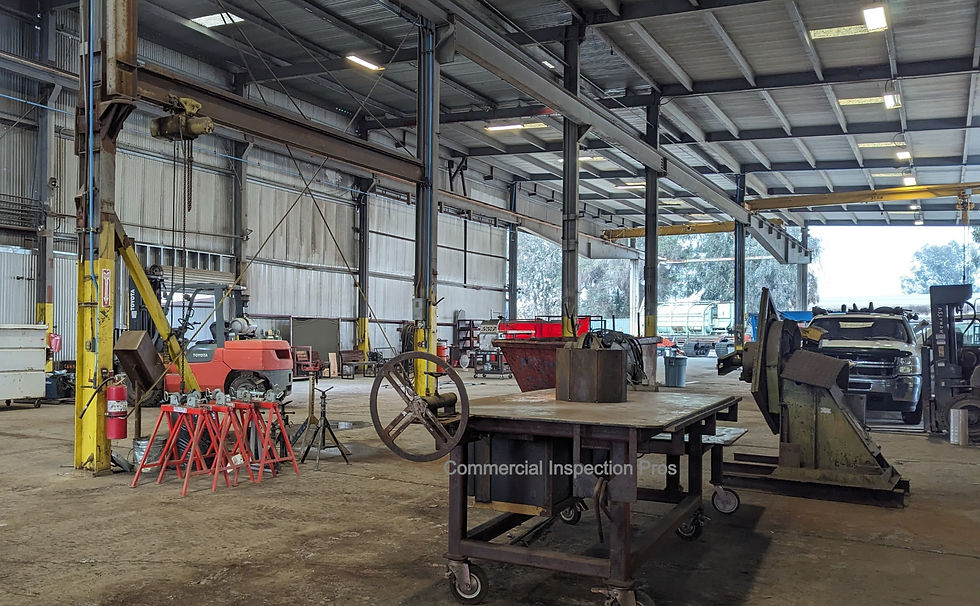
Choosing the Right Inspector:
Finding the right inspector is crucial. Look for someone with experience in inspecting manufacturing facilities, relevant certifications, and a strong understanding of safety regulations. References from past clients can also be helpful.
Making the Most of the Inspection:
To get the most out of your inspection, actively participate in the process. Ask questions, provide relevant information about the property, and express your concerns. This collaboration will help the inspector tailor their assessment to your specific needs and provide you with the most valuable insights.
Comments